jigs
Classify with absolute selectivity
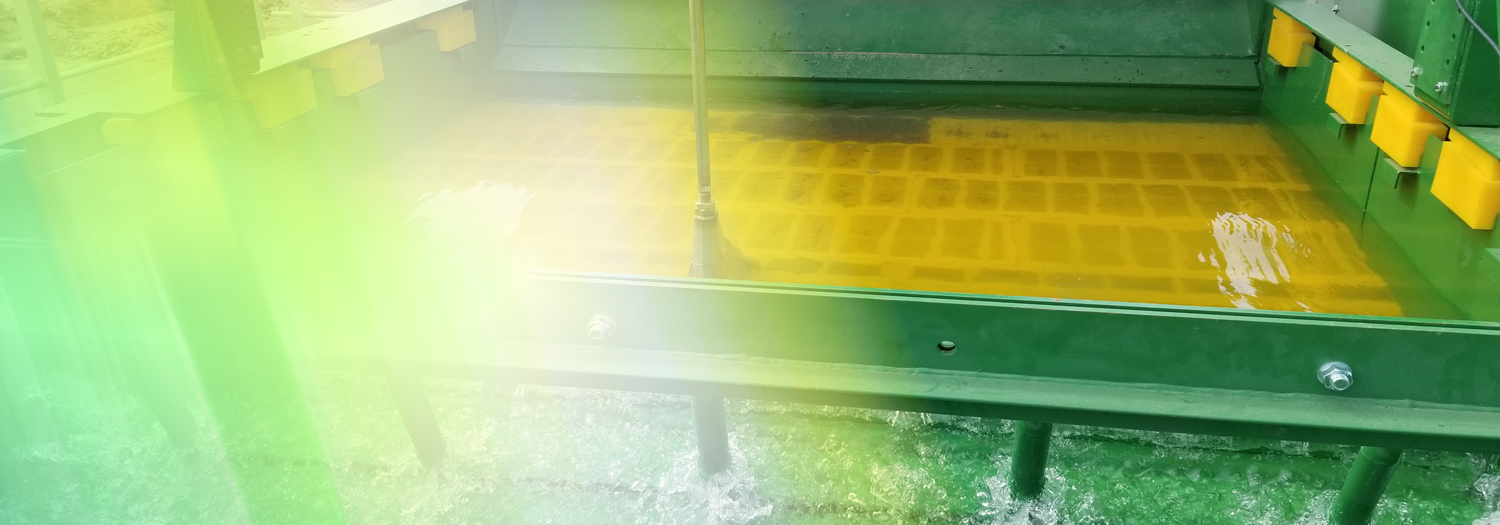
The precise jigs programme
Modern preparation plants must fulfil the increasing demands on raw material quality and the need to reuse primary or secondary raw materials. In addition to the selection of suitable components for sorting, new machines for classification ensure technical and therefore also economic success. If the materials responsible for the contamination have lower densities compared to the saleable raw material, sorting by density is a good option.
For this reason, STICHWEH jigs are being used in more and more preparation processes. STICHWEH jigs are built in co-operation with our partner, Snoby Separation Systems LLC, in Thüste.
Select a perfect fit
Efficient separation
Jigs separate according to the decisive characteristic "density". STICHWEH jigs impress with their high throughput capacity - up to 270 tonnes per hour - the use of precise operating data for selecting the process and for calculating the raw material quality in advance. Thanks to the automatic discharge control with analogue layer height measurement during operation, the STICHWEH jigs offer excellent results of the materials for further industrial use.
From sorting to discharging sand
To remove the light weight parts (bad material, e.g. coal, shale, iron oxide, pumice, shells ...), the material is placed on the jigs. A pulsed stream of water lifts the material and arranges it according to its density. The material layer is put into a loose, fluidised bed-like state by the pulsating upward flow of water. The light weight parts sink much slower than the heavy material and thus a layer formation takes place according to the density - i.e. the light weight parts come to the surface of the material bed, the heavy material collects in the lower part.
The separation of the light weight parts takes place in the upper area. The heavy weight parts are discharged below the light weight parts. Various discharge options are available depending on the grain size.
Jigs in use
When using STICHWEH jigs, the following requirements are met:
The normal sorting process remains simple, economical and ecologically efficient.
The selected sorting process
- enables a high degree of selectivity
- over the widest possible grain size range
- via a widely adjustable separation density
The integration of the sorting system ensures maximum operational reliability and a smooth process.
It functions
- with minimal personnel, energy and wear costs
- and settings customised to the site and raw material conditions
Media / Downloads
- Product film
- Product documentation